How Are Elevated Construction Costs Impacting Residential Development?
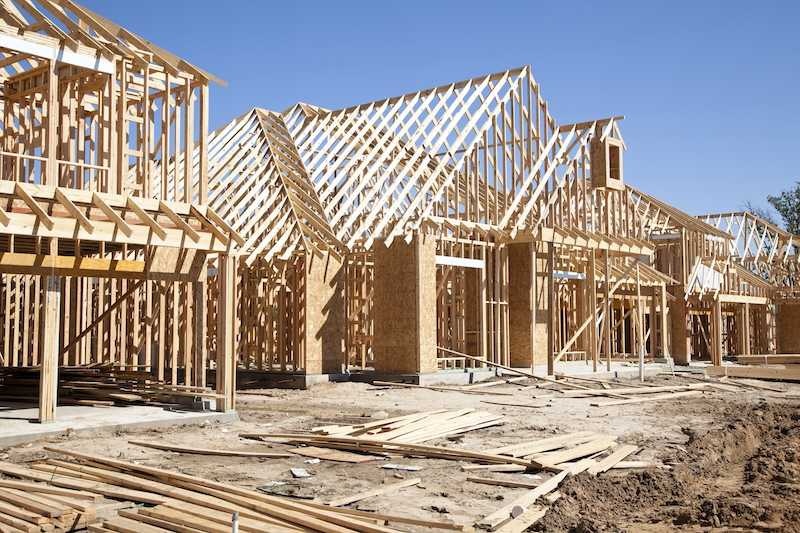
- Construction material prices were up 34.1% from one year ago through June.
- Many multifamily developers report downside business impacts because of rising supply costs.
- Construction’s labor recovery is failing to keep pace with rising demand for new housing units.
Key Findings
Before 2021, stubbornly high construction costs were already a source of frustration. Now, amid a housing demand boom and supply chain disruptions caused by the pandemic, construction costs have elevated from a concern to a significant issue. They are influencing project feasibility and construction timelines.
All told, the cost of building new inventory is exceptionally high. Appreciably higher construction costs associated with supply chain disruptions are likely transitory. They should abate as production of construction inputs continues to ramp back up. However, cost pressures due to increased competition for construction labor may not quickly self-correct, especially in metropolitan areas that are attracting new residents at a fast rate.
Material Construction Costs
The market value of any newly built housing unit depends on various factors. By examining the land value, cost of labor to construct the unit and material costs, the price tag of new construction can be broken down to the sum of its parts. According to the U.S. Bureau of Labor Statistics (BLS)’s June 2021 release of the Producer Price Index for construction materials, physical inputs were up a stunning 34.1% from the same time one year ago as of June 2021 (Chart 1). The previous record high for an annual increase was 21.4% in 1974 — when consumer prices were rising by more than 10% annually. Further, critical inputs such as lumber (+97.2%), iron and steel (+73.2%) and plywood (+144.5%) are all posting staggeringly higher prices than one year ago.
According to the latest National Multifamily Housing Council (NMHC) Construction Survey, the recent run-up in prices is having a meaningful impact on multifamily developers. Through the latest round of responses, 86% of developers reported that a lack of materials available was impacting their business (Chart 2).[1] Moreover, 100% of respondents reported seeing rising material costs and 69% of respondents reported experiencing a deal getting repriced up by more than 5%. Wait times for new supply could be longer in the future. Fifty six percent of respondents reported having construction delays due to changes in economic feasibility.
Speaking to GlobeSt, Thomas J. Bisacquino, president and CEO of NAIOP, cites that “the materials and supply chain issues are lagging effects of the pandemic, and they are affecting every industry.” As reported by NPR, the run up in lumber and plywood prices was not due to a shortage of timber, but rather a slowdown at sawmills. The NPR analysis notes that sawmills cut back on production early in the pandemic due to health concerns and an anticipated drop-off in orders. Of course, the pandemic had the opposite effect on demand than those sawmill operators initially anticipated, leaving them unable to keep up with surging orders.
Signs of Normalization
While supply shortages may be the single-largest source of elevated construction costs in 2021, they are also the factor most likely to see some normalization through the second half of the year as production stabilizes and housing-related demand, including renovations, begins to soften. According to the Board of Governors, wood product manufacturers were producing at 80.3% of capacity in January 2020, before falling as low 67.9% in April 2020. They were back to producing at 79.1% of capacity as of June 2021. Production is also catching back up for iron and steel product manufacturers. Capacity utilization for the industry started at 83.4% in January 2020, fell to a low of 52.6% in May 2020, and has since climbed to 83.5% through June 2021.
On the demand side, housing starts have remained relatively flat in recent months, but they are well above their 2019 average. June 2021 advance retail sales data from the U.S. Census Bureau showed spending at Building Materials, Garden Equipment and Supplies Dealers beginning to moderate but remaining above 2019 levels.
There is some evidence that increases in utilization and the stabilization in demand are starting to moderate prices. According to CME Group data, retrieved through Marketwatch, the price of 1,000 board feet of lumber was $648 through July 23, 2021, well above the relatively stable $320-$450 range it sat in from early 2019 through the start of the pandemic. However, this figure is a dramatic improvement from $1,670 peak recorded in May of this year.
Labor Market
When the U.S. went into its shutdown during the spring of 2020, there wasn’t a corner of the economy that went unscathed. More than 36 million Americans filed for first-time unemployment benefits between March and May, according to the BLS. U.S. payrolls are still down by 6.8 million workers from the month before the shutdown. The labor market’s road to recovery has been wholly uneven across different sectors — both in terms of outcomes and driving forces.
The construction industry experienced severe job losses that matched the national trend over the initial few months of the crisis. Between February and April 2020, the number of workers employed in construction jobs declined by 14.5%. Over the same period, residential builders, a subset of all construction workers, saw its number of employees decline by 15.6%. Put simply, no matter the type of project, the construction industry reacted to the shutdown in lockstep with the broader labor market, even as the U.S. Department of Homeland Security identified construction as an essential activity and 43 states adopted the recommendation either in full or with only limited exception.
As demand for new housing surged into the recovery, construction employment totals have recovered more quickly than the labor market generally. Through June 2021, the total number of employed nonfarm workers is 4.4% lower than it was in February 2020. For construction workers and homebuilders, the employment totals are 3.1% below and 3.9% above their February 2020 totals, respectively — both outperforming the broad labor market.[2]
Skilled Worker Shortages
One pressing challenge facing the construction labor market is that there are not enough skilled workers available to meet the demand for labor. According to the BLS Job Openings and Labor Turnover Survey (JOLTS), construction job openings totaled 299,000 in May 2021, almost directly in line with the 311,000 construction hires over the same period. Over the life of the JOLTS survey, which started collection in December 2000, the number of construction hires has, on average, exceeded construction openings by 230,000. This spread has consistently trended downward since 2011 (Chart 3), reflecting construction employers’ growing need to formally recruit talent and compete within a limited pool of skilled construction workers.
These data coincide with reports suggesting that hiring enough skilled construction labor to match demand is a clear challenge. According to the Association of General Contractors’ 2021 Construction Outlook Survey, many respondents expect tightening construction labor market conditions. Of those surveyed, 28% expect it will continue to be very difficult to hire personnel in 2021, while another 21% expect it will become more difficult (Chart 4). NAHB Chief Economist, Robert Dietz, shares these sentiments, claiming in a recent blog that he excepts that the scarcity for construction labor will only increase in the months ahead.
Hot Markets
The growing acceptance of workplace flexibility has allowed many workers to keep their gateway market jobs while moving into less expensive and more expansive housing setups. The fading requirement to be in the physical office five days a week is leading to higher levels of demand for single-family housing (including single-family rentals), especially for those workers in hybrid setups that want to remain reasonably close to the office.
For workers who can be entirely remote, the attractive combination of urban amenities and affordability in several Sun Belt metros is increasingly attracting migrants from Northern states.
Markets such as Austin and Nashville are recording a surge in residential building permits relative to their underlying market size. Measured across the top 50 metropolitan statistical areas by population, markets have permitted an average of 6.0 residential housing units per 1,000 residents in the 12 months ending in June 2021. For Austin, this total reaches up to 21.7 — 11.7 of which are in one- to four-family properties and 10.0 are in multifamily properties (Chart 5).
For Nashville, the total number of building permits over the past year per 1,000 residents reaches 16.1 — 9.1 in one- to four-family properties and 7.1 in multifamily properties. Issues impacting the broader construction industry are even more exacerbated in these high-growth markets, as illustrated in the latest release of the Federal Reserve’s Beige Book.
Demand for residential units in these markets is not limited to single-family homes. Seven of the top 10 markets for total residential permits were also in the top markets for total multifamily permits. The data show that the development pipelines in these metros are robust for both single-family and multifamily construction, reflecting the increased demand from both renters looking to transition to homeownership and traditional renters that are relocating.
Outlook
The construction industry has experienced pricing pressures over the past year. From the underlying building materials to the available pool of qualified labor, shortages are common throughout the development lifecycle. The rapid rise in construction costs has reached frustrating thresholds. In many cases, they are causing delays and even scrapped projects altogether.
On the material input side, there at least appears to be some relief in sight. Manufacturers have caught back up to their pre-pandemic levels of output in recent months. This should mean a re-anchoring of prices and a decline in volatility. However, prices for commodities such as lumber could potentially settle at levels above their pre-pandemic norms should housing starts keep their current pace over the short and medium term. According to the latest NAHB forecast, housing starts are forecast to exceed 2019 totals by at least 20% annually through 2023.
Finding enough skilled hands to match rising demand for new housing units may be a more deeply entrenched price pressure. This is especially true in markets experiencing a dramatic influx of new residents. It can take years for a market to adjust its housing stock to match a demand-side change. The acceleration of migration patterns as a result of the pandemic is magnifying the distortion. All else equal, the sheer number of headwinds will sustain high residential construction costs for at least the short term. Over the medium term, the process of bringing costs back down will depend on local factors.
[1] Latest round of NMHC Construction Survey (Round 7) was conducted between May 17 to June 1, 2021. Previous surveys were conducted as follows: Round 1 (March 27 to April 1, 2020); Round 2 (April 9 to April 14, 2020); Round 3 (May 11 to May 20, 2020); Round 4 ( July 6 to July 15, 2020); Round 5 (October 6 to October 27, 2020); and Round 6 (February 10 to March 5, 2021).
[2] Homebuilders are an employment subset of total construction employment.